Interior Design assistant professor’s team awarded National Science Foundation grant
CCA’s Dr. Negar Kalantar investigates a new construction material approach that could help buildings be more adaptable to erratic environment conditions.
Grant encourages high-risk, high-reward research
This summer, the National Science Foundation awarded CCA assistant professor and co-director of CCA Digital Craft Lab Negar Kalantar and a team of engineers a $69,999 Early-Concept Grant for Exploratory Research (EAGER). EAGER grants support potentially transformative or exploratory research that tackles new subjects, different methods, or interdisciplinary approaches.
Research by Kalantar’s team accomplishes all three. Their research proposal seeks to investigate a new approach for making building-skins and facades that can mold to various complex geometries, manipulate waves imparted to the buildings by natural disasters (such as hurricanes, tornadoes, and earthquakes), and dissipate energy from high-velocity winds. Moldability is a key feature of the material’s ability to sustain various extreme events and will be achieved by relief cutting, or “kerfing,” a technique in which a pattern is cut into a flat surface, leaving uncut elements raised and enabling flexible movement.
Kalantar’s work will explore if relief cutting solid wood or metal panels with certain microstructural patterns can be offered in a low-cost, accessible process—which would make it particularly well-suited for the building and construction industry—while also satisfying modern architecture’s shift beyond simple geometries toward complex freeform structures.
“A solution that simultaneously addresses all the above issues,” the team writes in its project abstract, “will require redefining some of the conventional paradigms in construction material design and deployment.”
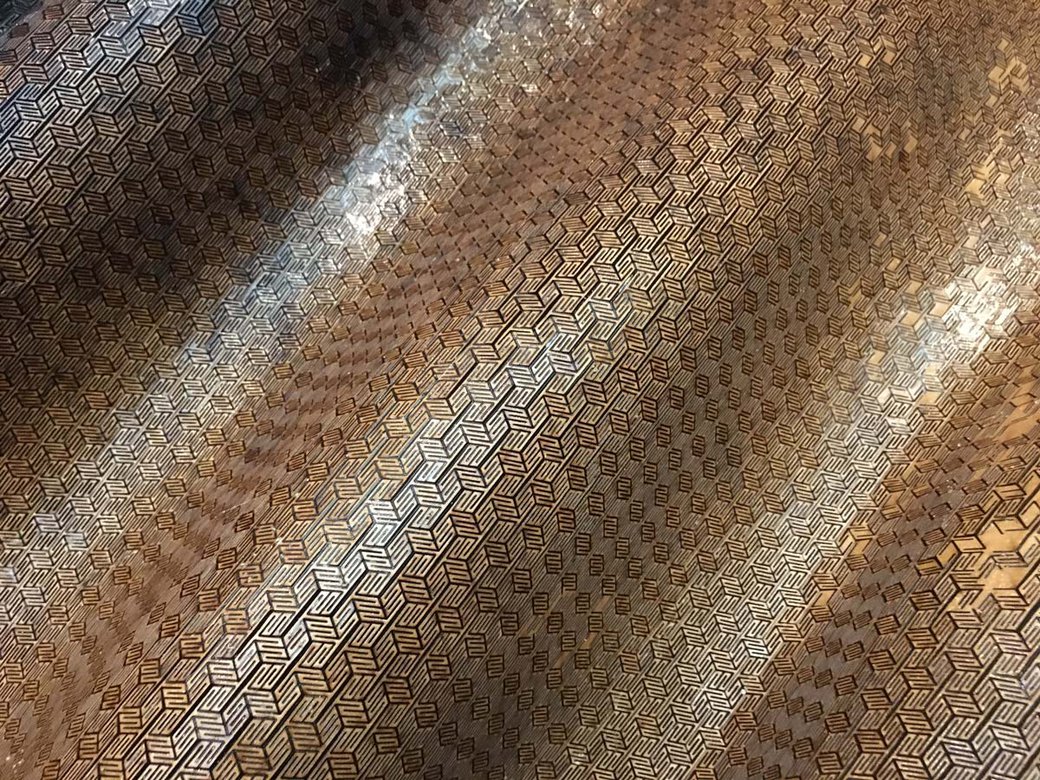
A wavy panel fabricated out of a flat MDF sheet. Photo courtesy of the research team.
A leap forward for structural engineering
Relief cutting turns rigid, flat panels into flexible materials. Kalantar will use the technique to endow thin material sheets with prescribed curved shapes and surface patterns. The objective of such patterning is two-fold. First, it allows for molding flat plates into a nearly endless array of complex freeform shapes, which will fulfill a variety of functional and aesthetic architectural needs. Second, it induces a microstructural geometry and property modulation that can help absorb and dissipate energy brought by a wide range of wave and vibration events, such as tsunamis and earthquakes.
Although relief cutting helps make surfaces more flexible, it can also reduce their load-carrying ability, which isn't ideal if the building is experiencing high-stress situations. The research will therefore “provide a means to potentially turn the disadvantage of the cutting method into an advantage,” the abstract explains. For example, how can the cut patterns enhance the dynamic properties of the panel so it better resists hazards?
“This research,” the abstract continues, “can advance structural engineering by pushing complex freeform shapes to a standard practice that intertwines aesthetic arguments, building performance requirements, and material design considerations.”
The team proposes that not only will this improve hazard mitigation strategies—actions taken to help reduce long-term risks caused by disasters like flooding, earthquakes, wildfires, landslides, or dam failure—but, “to a greater impact, freeform complex shapes can provide buildings with additional functionalities beyond their default load bearing and shelter capabilities.”
Delivering great potential human impact
The research has roots at Texas A&M University, where two years ago a team began investigating affordable methods of construction for complex geometries. The NSF-grant research, which kicked off in June 2019, is being conducted at CCA in collaboration with principal investigators from Texas A&M’s Department of Mechanical Engineering (Dr. Anastasia Muliana and Dr. Maria Koliou) and University of Minnesota’s Department of Civil, Environmental, and Geo-Engineering (Dr. Stefano Gonella).
According to the team’s proposal, they will study two scales of structural systems, such as components and buildings, as well as two types of materials with inherently different mechanical properties, such as wood and metal. Following a simulation-based design stage that explores the design space that relief cutting makes possible, Kalantar and team will fabricate, mold into shapes, and test the freeform components in the CCA Digital Craft Lab and Autodesk San Francisco Technology Center. This environment will mimic the dynamic loads of high velocity winds to imitate the stress and resulting deformation a material, as part of an actual architectural structure, can experience.
“My team already developed an algorithm for turning rigid planar panels into flexible ones. By changing parameters, we can control local properties of the pattern to obtain desired stiffness and flexibility in any given region,” Kalantar says. “This approach provides a simple interface to construct desired patterns and forms.”
“My team already developed an algorithm for turning rigid planar panels into flexible ones.”
Interior Design Assistant Professor
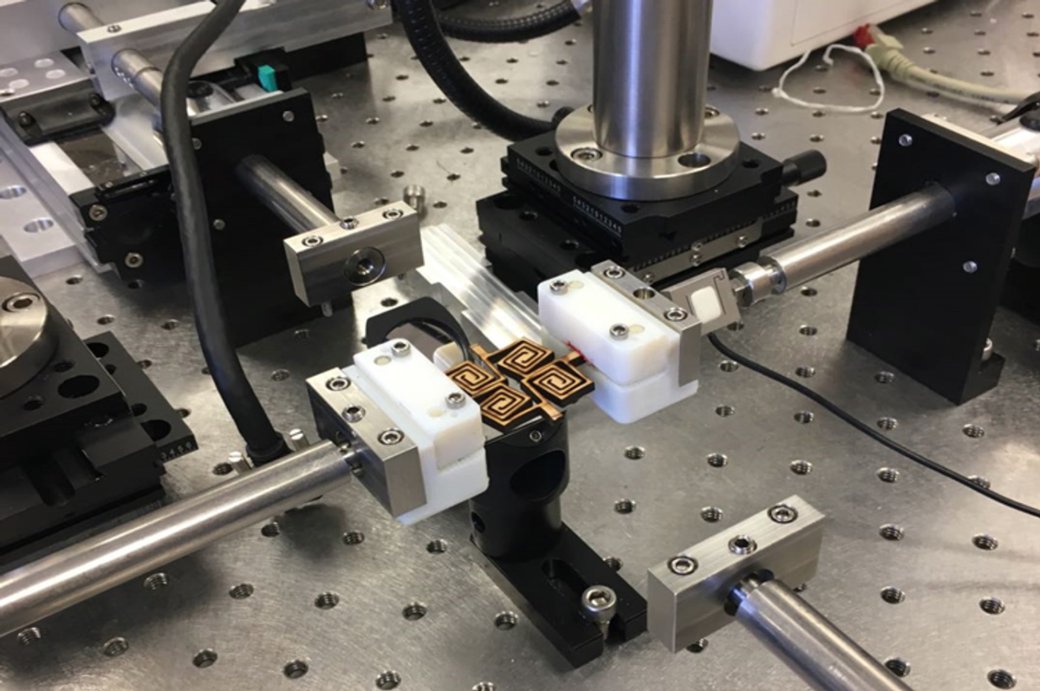
Simulated MDF kerf unit-cells and panels designed by Negar Kalantar, CCA interior design professor, are tested on a custom-built a mechanical system developed at Texas A&M University.
Graduate and undergraduate students at CCA have tried the techniques on medium density fiberboard (MDF) and plywood and are currently working on applying the techniques to stainless steel sheets, Kalantar says. Meanwhile, Muliana and her Texas A&M team have simulated the MDF kerf unit-cells and panels, and custom-built a mechanical testing system. The other principal investigators are working on defining structural analyses under static and dynamic loadings.
“This study,” Kalantar says, “will reveal whether the proposed construction materials can efficiently manage or dissipate the energy dynamically imparted to buildings—as opposed to simply resisting loads, as in conventional buildings—while featuring their required architectural attributes.”
Equipping buildings with the ability to redirect, localize, trap, and dissipate energy, instead of merely resisting the impacting forces, can lead to a more efficient hazard mitigation strategy, save money in damages, and potentially even save lives—all while creating a more aesthetically beautiful landscape.
We caught up with Kalantar to further discuss the research, what she’s excited about, and what she hopes will result when the study concludes in 2021.
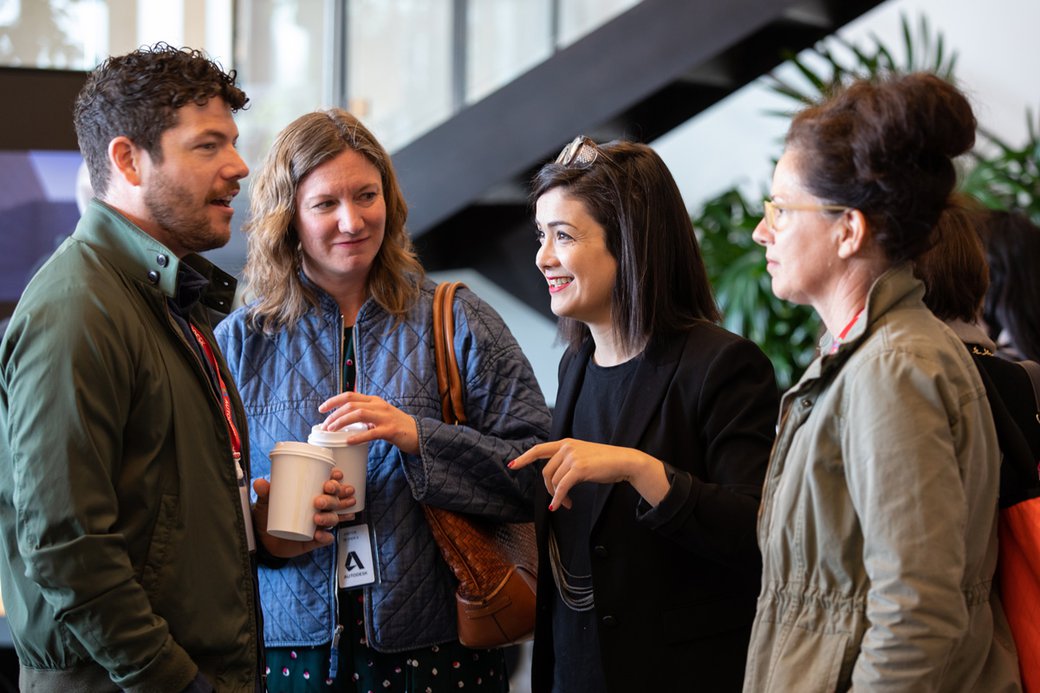
Photo by Nicholas Lea Bruno/CCA
Q and A with assistant professor Negar Kalantar
What is your background in relief cutting?
For the last couple of years, we’ve been investigating two challenges that designers deal with in the context of geometric complexity and finding form. Despite the widespread development and adoption of 3D modeling software that allows for the virtual design of complicated shapes, the physical construction of such shapes remains an unsolved problem; currently, it requires advanced machinery capable of milling custom 3D features or 3D printing. However, the most readily available digital fabrication tool continues to be the laser cutter and waterjet, and most construction materials come as sheets. These materials possess sufficient strength for structural integrity, but they are relatively stiff, making it difficult to form them into complex curved shapes.
Even when it’s possible to form complex shapes like in sheet metal forming, the cost of fabricating individual panels of unique shapes will be extremely high. For materials that are fabricated with molds, the idea of reusable molds will potentially reduce the construction cost and waste. However, the reusable mold is still labor intensive. The complexity in generating freeform shapes is further alleviated by the large variations in the mechanical and non-mechanical behaviors of different materials. It is then necessary to incorporate structural analyses during the design stage instead of mainly focusing on achieving complex geometries.
One of the practical methods to create flexible planar surfaces from relatively stiff materials like metals, wood, and medium density fiberboard (MDF) is relief cutting or kerfing. This approach allows for utilizing mass produced materials of standard shape and size in generating flexible structures with complex geometries.
Interior Design program achievements
Why is this research important to you?
As a design thinker, I look forward to contributing to some fundamental design questions that we are dealing with today. One of the most important is how unpredictable weather patterns have led to more severe and frequent natural disasters. While stopping natural disasters is not an option, buildings should be designed with the ability to mitigate the impact of such hazards. I’m hoping this research can offer an intelligent and unique hazard mitigation strategy that manipulates wave patterns and minimizes forces impacted on the buildings, which are not seen in conventional approaches. To a greater impact, when freeform complex shapes become a part of everyday experience, they will provide buildings with additional functionalities beyond their default load bearing and shelter capabilities.
As a design thinker, I look forward to contributing to some fundamental design questions that we are dealing with today. … While stopping natural disasters is not an option, buildings should be designed with the ability to mitigate the impact of such hazards.”
How does this research connect to your pedagogy at CCA?
I strongly believe that the scholarship of design starts from early design studios, therefore I usually engage my students in the process of the research. My goal is [to have] our students think about the materiality and fabrication process from the early stage of design. My students are the primary users of the developed platform. I will integrate the design of kerf freeform shapes into my studio projects. Students will be trained on using differential geometry and computer graphics to generate various forms of complex shapes and at the same time they should have plans on realizing their design, which is based on the materials they’ll use.
What would success look like for this research?
This research is high-risk and high-reward in that it represents a drastic departure from traditional construction methodologies: It will lead to a paradigm shift in building design, in which freeform complex shapes are demonstrated to offer superior resistance to dynamic loadings; it introduces a new and bold modular fabrication philosophy for freeform shapes that will generate minimal material waste, eliminate the need for mold casting, and simplify the logistics of material transportation; and it harmoniously blends dynamic performance and architectural constraints—two requirements that are often perceived to be mutually exclusive—by taking advantage of the intrinsic mechanical and aesthetic attributes of complex shapes and microstructural patterns.
Pursue your creative practice within a supportive community